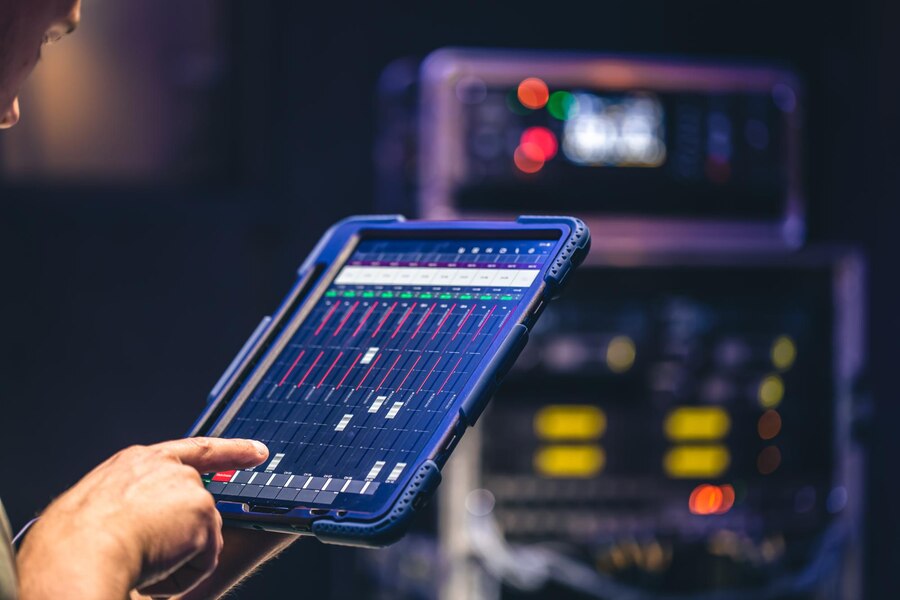
Machine Condition Monitoring Market Report By Component (Hardware, Software, Services), By Monitoring Technique (Vibration Monitoring, Ultrasound Monitoring, Thermography, Oil Analysis, Motor Current Analysis, Others), By Deployment Type (On-premises, Cloud-based), By End User Industry, By Region and Companies - Industry Segment Outlook, Market Assessment, Competition Scenario, Trends and Forecast 2024-2033
-
46775
-
May 2024
-
321
-
-
This report was compiled by Correspondence Linkedin | Detailed Market research Methodology Our methodology involves a mix of primary research, including interviews with leading mental health experts, and secondary research from reputable medical journals and databases. View Detailed Methodology Page
-
Quick Navigation
Report Overview
The Global Machine Condition Monitoring Market size is expected to be worth around USD 6.4 Billion by 2033, from USD 3.1 Billion in 2023, growing at a CAGR of 7.8% during the forecast period from 2024 to 2033.
The Machine Condition Monitoring Market focuses on technologies that monitor the health and performance of industrial machinery. These systems detect potential issues early, preventing costly downtime and extending equipment lifespan. Key technologies include vibration analysis, thermal imaging, and oil analysis.
Market growth is driven by increased automation, the need for operational efficiency, and advancements in predictive maintenance. Industries like manufacturing, energy, and transportation rely on these solutions. Leading companies invest in advanced sensors and AI-driven analytics to enhance monitoring accuracy. The machine condition monitoring market is vital for maintaining industrial productivity and reducing maintenance costs.
The Machine Condition Monitoring Market is poised for strong growth, driven by the increasing adoption of predictive maintenance strategies. In recent years, the use of predictive maintenance has risen from 47% in 2017 to 51% in 2018. Despite this growth, preventive maintenance remains the preferred approach for 80% of maintenance personnel. However, manufacturers who implement predictive maintenance strategies maximize their throughput and achieve cost savings of up to 40% compared to those using traditional maintenance methods.
Predictive maintenance relies on advanced monitoring technologies to assess machine conditions and predict potential failures. This approach enables manufacturers to address issues before they lead to costly downtime, thereby improving operational efficiency and extending the lifespan of machinery. The shift towards predictive maintenance is driven by the increasing need to optimize production processes and reduce maintenance costs.
The growing complexity of modern manufacturing systems and the rising emphasis on operational efficiency further fuel the demand for machine condition monitoring solutions. These solutions provide real-time insights into equipment health, allowing for timely interventions and minimizing unexpected breakdowns.
Market players are expected to focus on developing innovative and scalable condition monitoring technologies to meet the evolving needs of the manufacturing sector. The integration of IoT, AI, and machine learning into condition monitoring systems will enhance their predictive capabilities and drive market growth.
Overall, the Machine Condition Monitoring Market presents significant opportunities for growth, supported by the ongoing trend towards predictive maintenance and the continuous advancements in monitoring technologies. As manufacturers increasingly recognize the benefits of predictive maintenance, the demand for sophisticated condition monitoring solutions is set to rise, ensuring a promising market outlook.
Key Takeaways
- Market Value: The Global Machine Condition Monitoring Market is expected to be worth USD 6.4 billion by 2033, from USD 3.1 billion in 2023, with a CAGR of 7.8%.
- Component Analysis: Hardware dominates with 50%; essential for real-time data capture.
- Monitoring Technique Analysis: Vibration monitoring dominates with 40%; effective for detecting mechanical faults.
- Deployment Type Analysis: On-premises deployment dominates with 60%; need for data control and integration.
- End User Industry Analysis: Manufacturing dominates with 35%; high demand for equipment reliability.
- Dominant Region: North America with 39.6%; advanced industrial infrastructure.
- High Growth Region: Europe; growth driven by technological adoption.
- Analyst Viewpoint: The market is competitive with significant growth potential. Future advancements in sensor technology and data analytics will drive market expansion.
- Growth Opportunities: Leveraging IoT and AI technologies can enhance predictive maintenance and create new market opportunities.
Driving Factors
Increasing Adoption of Predictive Maintenance Strategies Drives Market Growth
Predictive maintenance is gaining traction across various industries due to its ability to optimize asset performance, reduce downtime, and lower maintenance costs. Machine condition monitoring systems play a crucial role in enabling predictive maintenance by continuously monitoring equipment health and detecting potential failures before they occur. This proactive approach helps in identifying issues before they lead to significant damage or operational disruptions.
In the manufacturing sector, companies like Siemens and Emerson have successfully implemented machine condition monitoring solutions to enhance their production processes and minimize unplanned downtime. By utilizing these systems, manufacturers can anticipate equipment failures and schedule maintenance activities during planned downtimes, thereby avoiding unexpected production halts.
The benefits of predictive maintenance extend beyond manufacturing. For instance, in the oil and gas industry, companies like BP and Shell use machine condition monitoring to ensure the reliable operation of critical equipment such as pumps, turbocompressors, and turbines. This not only improves operational efficiency but also extends the lifespan of expensive assets, leading to significant cost savings.
Rising Focus on Asset Optimization and Operational Efficiency Drives Market Growth
Organizations are increasingly focused on maximizing the efficiency and lifespan of their assets to reduce operational costs and improve profitability. Machine condition monitoring systems provide valuable insights into asset health, enabling proactive maintenance and optimizing asset utilization. This focus on asset optimization is a key driver for the growth of the machine condition monitoring market.
In the oil and gas industry, companies like ExxonMobil and Chevron have deployed machine condition monitoring systems to optimize the performance of their critical equipment. By continuously monitoring the condition of pumps, compressors, and turbines, these companies can detect signs of wear and tear early and perform maintenance before equipment failure occurs. This not only reduces downtime but also enhances the operational efficiency of their production processes.
The benefits of asset optimization are evident in other industries as well. For example, in the power generation sector, companies like General Electric and Siemens use machine condition monitoring to ensure the smooth operation of turbines and generators. By maintaining optimal performance levels, these companies can achieve higher energy efficiency and reduce operational costs.
Advancement in Sensor Technology and Data Analytics Drives Market Growth
The development of advanced sensors and data analytics has significantly enhanced machine condition monitoring capabilities. Advanced sensors, such as vibration sensors, temperature sensors, and acoustic emission sensors, facilitate more accurate and real-time data collection. These sensors, combined with sophisticated data analytics and machine learning development algorithms, enable more effective data processing and pattern recognition, improving the ability to detect anomalies and predict potential failures.
Companies like SKF and Fluke are at the forefront of this technological advancement. They offer advanced machine condition monitoring solutions that leverage cutting-edge sensor technology and data analytics. For instance, SKF’s monitoring systems use vibration sensors to detect early signs of mechanical issues, allowing for timely maintenance interventions. Similarly, Fluke's solutions utilize temperature sensors to monitor equipment health, ensuring optimal performance.
The integration of machine learning algorithms further enhances the predictive capabilities of these systems. By analyzing large volumes of data, these algorithms can identify patterns and trends that indicate potential equipment failures, enabling more accurate and reliable predictions. This technological advancement has a profound impact on various industries, including manufacturing, oil and gas, and power generation.
Restraining Factors
High Initial Investment Costs Restrain Market Growth
Implementing a comprehensive machine condition monitoring system involves significant upfront costs. These costs include expenses for hardware (sensors, data acquisition systems), software, and integration. This high initial investment can be a major barrier for small and medium-sized enterprises (SMEs) with limited budgets.
In price-sensitive industries or regions, this issue is particularly pronounced. For instance, smaller manufacturing facilities or agricultural operations may struggle to adopt advanced machine condition monitoring solutions due to the associated costs. According to industry reports, the initial investment for such systems can range from $50,000 to $200,000, depending on the complexity and scale of the operation.
These high costs can deter many potential users, limiting the overall market growth. Companies must weigh the benefits of these systems against the substantial initial expenditure, which can be a challenging decision for those with constrained financial resources.
Lack of Skilled Personnel and Technical Expertise Restrains Market Growth
Effective implementation and maintenance of machine condition monitoring systems require skilled personnel with specialized knowledge. This includes expertise in vibration analysis, data interpretation, and predictive maintenance strategies. Many organizations, especially in developing regions, struggle to find and retain such skilled professionals.
The lack of technical expertise can hinder the widespread adoption of machine condition monitoring solutions. Companies might need to invest in extensive training programs or outsource expertise, which adds to the overall costs. According to a recent survey, over 60% of organizations reported difficulties in finding qualified personnel to manage their condition monitoring systems.
This shortage of skilled workers not only increases operational costs but also delays the implementation of these systems. As a result, the potential benefits of machine condition monitoring are not fully realized, restricting market growth and limiting its adoption across various industries.
Component Analysis
Hardware segment dominates with 50% due to the essential role of sensors and data acquisition systems in capturing real-time equipment health data.
The Machine Condition Monitoring Market can be segmented by components into hardware, software, and services. The hardware segment dominates, holding a significant market share due to the widespread use of sensors, probes, and data acquisition systems. Hardware components are essential for capturing real-time data on equipment health, which is critical for predictive maintenance. Sensors, such as vibration and temperature sensors, are integral to these systems, providing the necessary inputs for condition monitoring. Data acquisition systems then collect and process this data, enabling the detection of potential equipment failures.
This dominance is attributed to the continuous advancements in sensor technology and the growing need for accurate and reliable data. Companies like SKF and Emerson are leading the market with their innovative sensor solutions, which offer enhanced sensitivity and durability. These advancements help in reducing downtime and maintenance costs, making hardware an indispensable part of machine condition monitoring systems.
The software segment, including data analysis software and reporting and visualization tools, is also crucial. These tools help interpret the vast amounts of data collected by hardware components. The software segment is growing rapidly, driven by the increasing adoption of advanced data analytics and machine learning algorithms. These technologies enhance the predictive capabilities of condition monitoring systems, allowing for more accurate and timely maintenance decisions. Despite its growth, the software segment still lags behind hardware in terms of market share.
The services segment, which includes installation, integration, maintenance, support, and consulting, plays a supportive role. These services ensure the effective deployment and operation of machine condition monitoring systems. While services contribute significantly to the overall market, they account for a smaller share compared to hardware and software. The necessity for skilled personnel and ongoing support services is a key driver for this segment, particularly as more companies adopt condition monitoring technologies.
Monitoring Technique Analysis
Vibration monitoring dominates with 40% due to its effectiveness in detecting mechanical faults in rotating equipment.
The Machine Condition Monitoring Market is segmented by monitoring technique, including vibration monitoring, ultrasound monitoring, thermography, oil analysis, motor current analysis, and others. Vibration monitoring dominates this segment due to its effectiveness in detecting mechanical faults in rotating equipment. This technique is widely used in industries such as manufacturing, oil and gas, and power generation, where machinery reliability is critical.
This dominance is driven by the technique’s ability to identify imbalances, misalignments, and bearing faults early, preventing costly breakdowns and downtime. Companies like SKF and Emerson provide advanced vibration monitoring solutions that offer high accuracy and real-time data, making them essential for maintaining equipment health.
Other monitoring techniques, such as ultrasound monitoring and thermography, also play significant roles. Ultrasound monitoring is effective in detecting issues in slow-speed machinery and identifying leaks in compressed air systems. Thermography, which uses infrared cameras to detect temperature variations, helps identify overheating components and electrical faults. These techniques, while not as widely adopted as vibration monitoring, are gaining traction due to their specific applications and benefits.
Oil analysis and motor current analysis are also important. Oil analysis helps detect contaminants and wear particles in lubricants, indicating potential issues in engines and hydraulic systems. Motor current analysis monitors electrical signals in motors to identify faults like winding issues and rotor bar problems. These techniques complement vibration monitoring, providing a comprehensive approach to machine condition monitoring.
Deployment Type Analysis
On-premises deployment dominates with 60% due to the need for data control and integration within existing IT infrastructure.
The Machine Condition Monitoring Market is segmented by deployment type into on-premises and cloud-based solutions. On-premises deployment dominates this segment due to the need for direct control over data and system integration within existing IT infrastructure. This type of deployment is preferred by industries with stringent data security requirements, such as aerospace and defense, and oil and gas.
The preference for on-premises deployment is driven by the ability to maintain data confidentiality and control over system customization. Companies like General Electric and Honeywell offer robust on-premises condition monitoring systems that integrate seamlessly with existing enterprise systems, ensuring data integrity and operational continuity.
Cloud-based deployment, although growing rapidly, holds a smaller market share. Cloud-based solutions offer advantages such as remote access, scalability, and reduced upfront costs. These benefits make cloud-based deployment attractive for SMEs and industries with distributed operations. The flexibility and cost-effectiveness of cloud-based solutions are driving their adoption, particularly in the manufacturing and automotive sectors. However, concerns over data security and internet dependency remain barriers to widespread adoption.
End User Industry Analysis
Manufacturing industry dominates with 35% due to the high demand for maintaining equipment reliability and reducing downtime.
The Machine Condition Monitoring Market is segmented by end user industry, including manufacturing, oil and gas, power generation, aerospace and defense, automotive, chemical and petrochemical, mining and metals, food and beverage, and others. The manufacturing industry dominates this segment due to the high demand for maintaining equipment reliability and reducing downtime.
This dominance is driven by the need for continuous production and minimizing unplanned downtime. Machine condition monitoring systems help manufacturers maintain optimal equipment performance, ensuring smooth and efficient operations. Companies like Siemens and Bosch have implemented advanced monitoring systems to enhance their manufacturing processes, resulting in significant cost savings and productivity improvements.
Other industries, such as oil and gas and power generation, also contribute significantly to market growth. The oil and gas industry uses machine condition monitoring to ensure the reliability of critical equipment like pumps and compressors. In power generation, monitoring systems help maintain the efficiency of turbines and generators. These industries require high equipment reliability due to the critical nature of their operations.
The aerospace and defense, automotive, chemical and petrochemical, mining and metals, and food and beverage industries also play vital roles. These industries benefit from reduced maintenance costs and improved operational efficiency through the use of machine condition monitoring systems. The diverse applications across these industries underscore the broad utility and impact of condition monitoring technologies.
Key Market Segments
By Component
- Hardware
- Software
- Services
By Monitoring Technique
- Vibration Monitoring
- Ultrasound Monitoring
- Thermography
- Oil Analysis
- Motor Current Analysis
- Others
By Deployment Type
- On-premises
- Cloud-based
By End User Industry
- Manufacturing
- Oil and Gas
- Power Generation
- Aerospace and Defense
- Automotive
- Chemical and Petrochemical
- Mining and Metals
- Food and Beverage
- Others
Growth Opportunities
Development of Cost-Effective and Scalable Solutions Offers Growth Opportunity
Developing cost-effective and scalable machine condition monitoring solutions presents a significant growth opportunity. Small and medium-sized enterprises (SMEs) often face budget constraints and find traditional monitoring solutions complex and expensive. By creating affordable and user-friendly systems, vendors can tap into this underserved market.
Companies like Pruftechnik and Fluke have introduced entry-level machine condition monitoring solutions designed specifically for SMEs. These solutions allow SMEs to implement predictive maintenance strategies without substantial investments. The demand for such cost-effective solutions is high, given that SMEs make up a large portion of the global industrial landscape.
According to market research, the adoption of scalable and affordable solutions could increase the overall market size by 20% over the next five years. This expansion highlights the potential for significant growth by addressing the needs of smaller enterprises.
Expansion into Emerging Industries and Applications Offers Growth Opportunity
Expanding machine condition monitoring into emerging industries and applications presents substantial growth opportunities. Traditional industries like manufacturing, oil and gas, and power generation have long adopted these solutions. However, emerging sectors such as renewable energy offer new potential.
The renewable energy sector, including wind and solar farms, can benefit greatly from machine condition monitoring. Monitoring solutions for wind turbine gearboxes and bearings, provided by companies like Romax and VibroBem, enable predictive maintenance and optimize energy production. This ensures the longevity and efficiency of renewable energy assets management.
With the renewable energy market projected to grow by 10% annually, the integration of machine condition monitoring in this sector could drive significant market expansion. This approach not only supports sustainable energy production but also opens new revenue streams for monitoring solution providers.
Trending Factors
Adoption of Industry 4.0 and Smart Manufacturing Are Trending Factors
The adoption of Industry 4.0 and smart manufacturing is a trending factor driving the machine condition monitoring market. As factories become more digitized and interconnected, the need for real-time monitoring and data-driven decision-making increases.
Machine condition monitoring systems are essential for enabling predictive maintenance, optimizing asset utilization, and improving manufacturing efficiency. Companies like Siemens and Rockwell Automation lead in offering Industry 4.0-compatible monitoring solutions that integrate seamlessly with smart factory environments.
Recent data shows that the smart manufacturing market is expected to grow at a CAGR of 12% from 2021 to 2026. This trend underscores the increasing importance of machine condition monitoring in modern industrial settings, as real-time data and advanced analytics become pivotal for operational success.
Rise of Artificial Intelligence (AI) and Machine Learning (ML) Are Trending Factors
The rise of AI and ML in machine condition monitoring is another trending factor. These advanced technologies enable more accurate anomaly detection, pattern recognition, and failure prediction by analyzing vast amounts of sensor data.
Companies like SKF and Honeywell leverage AI and ML algorithms in their monitoring solutions, providing enhanced diagnostic capabilities and predictive maintenance insights. AI and ML improve the accuracy and reliability of condition monitoring systems, making them indispensable for modern industries.
As AI and ML technologies become more accessible and affordable, their application in machine condition monitoring is expected to expand. Market projections indicate that the integration of AI and ML could enhance the efficiency of monitoring systems by up to 30%, driving further adoption and innovation in the industry.
Regional Analysis
North America Dominates with 39.6% Market Share
North America's dominance in the machine condition monitoring market is driven by several factors. The region has a high concentration of advanced industries like manufacturing, oil and gas, and power generation. These industries demand reliable condition monitoring systems to maintain operational efficiency and reduce downtime.
Additionally, North America has a well-established infrastructure for technological innovation and adoption. Companies like General Electric and Emerson are leading providers in this region, offering state-of-the-art solutions. The strong focus on predictive maintenance and the presence of key market players contribute significantly to North America's high market share.
Regional characteristics such as advanced industrialization and strong economic growth play a crucial role in the machine condition monitoring market. North America's robust infrastructure supports the widespread adoption of advanced monitoring technologies.
Market Share or Growth Rate in Other Regions
Europe:
Europe holds a significant share of the machine condition monitoring market, accounting for approximately 30% of the global market. The region's focus on industrial automation and stringent regulatory standards drive the adoption of advanced monitoring solutions. Key countries like Germany, the UK, and France are leading the market with substantial investments in manufacturing and energy sectors.Asia Pacific:
Asia Pacific is experiencing rapid growth in the machine condition monitoring market, with a current market share of about 20%. The region's growth is fueled by expanding industrialization and increasing adoption of automation technologies in countries like China, Japan, and India. The market in Asia Pacific is expected to grow at a CAGR of 10% over the next five years, making it one of the fastest-growing regions.Middle East & Africa:
The Middle East & Africa hold a smaller share of the global market, around 6%. The region's market growth is driven by the oil and gas industry, which heavily relies on machine condition monitoring for maintaining equipment reliability. Increasing investments in infrastructure and industrial projects are expected to boost market growth in the coming years.Latin America:
Latin America accounts for approximately 4.4% of the global machine condition monitoring market. The region's market is driven by industries such as mining, oil and gas, and manufacturing. Countries like Brazil and Mexico are leading the market, with growing investments in industrial automation and predictive maintenance technologies.Summary:
North America's leadership in machine condition monitoring is due to its advanced industries and robust infrastructure, maintaining a 39.6% market share. Europe follows with 30%, driven by automation and regulatory standards. Asia Pacific is rapidly growing at 20%, with a projected CAGR of 10%. The Middle East & Africa and Latin America hold 6% and 4.4%, respectively, influenced by sector-specific demands and regional developments.Key Regions and Countries
- North America
- The US
- Canada
- Mexico
- Western Europe
- Germany
- France
- The UK
- Spain
- Italy
- Portugal
- Ireland
- Austria
- Switzerland
- Benelux
- Nordic
- Rest of Western Europe
- Eastern Europe
- Russia
- Poland
- The Czech Republic
- Greece
- Rest of Eastern Europe
- APAC
- China
- Japan
- South Korea
- India
- Australia & New Zealand
- Indonesia
- Malaysia
- Philippines
- Singapore
- Thailand
- Vietnam
- Rest of APAC
- Latin America
- Brazil
- Colombia
- Chile
- Argentina
- Costa Rica
- Rest of Latin America
- Middle East & Africa
- Algeria
- Egypt
- Israel
- Kuwait
- Nigeria
- Saudi Arabia
- South Africa
- Turkey
- United Arab Emirates
- Rest of MEA
Key Players Analysis
The Machine Condition Monitoring market is led by several key companies that play crucial roles in shaping industry trends and technologies. Emerson Electric Co., General Electric Company, and Siemens AG are leading players, recognized for their comprehensive monitoring solutions and advanced analytics capabilities. These companies significantly impact the market by driving innovation and setting high standards for reliability and performance.
Honeywell International Inc., SKF Group, and Rockwell Automation, Inc. also hold strong positions in the market. They are known for their robust product offerings that include sensors and systems for detecting various machine anomalies. Their strategic focus on connectivity and data integration enhances their competitive edge, allowing for proactive maintenance strategies.
Companies like Parker Hannifin Corporation, ABB Ltd., and National Instruments Corporation contribute to the market with specialized technologies and customized solutions. Their products are integral in diverse industries, from manufacturing to aerospace, highlighting their role in broad market applications.
Smaller firms, such as Brüel & Kjær Vibro GmbH, Meggitt PLC, and Azima DLI Corporation, emphasize niche markets and specific monitoring needs, such as vibration analysis and thermal imaging. Their targeted approaches allow them to meet unique customer demands effectively.
Finally, ALS Limited, Analog Devices, Inc., and Fluke Corporation excel in providing supporting technologies and services that complement machine condition monitoring systems. These companies enhance the market's dynamism by offering tools that facilitate accurate data collection and analysis.
Overall, the key players in the Machine Condition Monitoring market are integral in advancing technology, expanding applications, and providing solutions that improve machine efficiency and safety across multiple industries. Their collective efforts not only lead market trends but also foster a more predictive maintenance environment.
Market Key Players
- Emerson Electric Co.
- General Electric Company
- Honeywell International Inc.
- SKF Group
- National Instruments Corporation
- Parker Hannifin Corporation
- Rockwell Automation, Inc.
- Siemens AG
- ABB Ltd.
- Brüel & Kjær Vibro GmbH
- Meggitt PLC
- ALS Limited
- Analog Devices, Inc.
- Fluke Corporation
- Azima DLI Corporation
Recent Developments
- February 2024: Advanced Technology Services (ATS) has enhanced its Reliability 360® Machine Health Monitoring platform, emphasizing user experience and efficiency with streamlined asset-level monitoring and remote sensor updates. These updates reflect ATS's commitment to customer-driven innovation.
- November 2023: Worldsensing launched the Vibration Meter, a wireless sensor with a tri-axial accelerometer, extended battery life, and LoRa connectivity. It aids compliance with industry standards and protects infrastructure from high-vibration activities.
- November 2023: Banner Engineering has launched a new suite of products for industrial monitoring, facilitating predictive maintenance and maximizing uptime. The systems include wired and wireless sensors, with easy setup and operation for minimal risk.
Report Scope
Report Features Description Market Value (2023) USD 3.1 Billion Forecast Revenue (2033) USD 6.4 Billion CAGR (2024-2033) 7.8% Base Year for Estimation 2023 Historic Period 2018-2023 Forecast Period 2024-2033 Report Coverage Revenue Forecast, Market Dynamics, Competitive Landscape, Recent Developments Segments Covered By Component (Hardware, Software, Services), By Monitoring Technique (Vibration Monitoring, Ultrasound Monitoring, Thermography, Oil Analysis, Motor Current Analysis, Others), By Deployment Type (On-premises, Cloud-based), By End User Industry (Manufacturing, Oil and Gas, Power Generation, Aerospace and Defense, Automotive, Chemical and Petrochemical, Mining and Metals, Food and Beverage, Others) Regional Analysis North America - The US, Canada, & Mexico; Western Europe - Germany, France, The UK, Spain, Italy, Portugal, Ireland, Austria, Switzerland, Benelux, Nordic, & Rest of Western Europe; Eastern Europe - Russia, Poland, The Czech Republic, Greece, & Rest of Eastern Europe; APAC - China, Japan, South Korea, India, Australia & New Zealand, Indonesia, Malaysia, Philippines, Singapore, Thailand, Vietnam, & Rest of APAC; Latin America - Brazil, Colombia, Chile, Argentina, Costa Rica, & Rest of Latin America; Middle East & Africa - Algeria, Egypt, Israel, Kuwait, Nigeria, Saudi Arabia, South Africa, Turkey, United Arab Emirates, & Rest of MEA Competitive Landscape Emerson Electric Co., General Electric Company, Honeywell International Inc., SKF Group, National Instruments Corporation, Parker Hannifin Corporation, Rockwell Automation, Inc., Siemens AG, ABB Ltd., Brüel & Kjær Vibro GmbH, Meggitt PLC, ALS Limited, Analog Devices, Inc., Fluke Corporation, Azima DLI Corporation Customization Scope Customization for segments, region/country-level will be provided. Moreover, additional customization can be done based on the requirements. Purchase Options We have three licenses to opt for: Single User License, Multi-User License (Up to 5 Users), Corporate Use License (Unlimited User and Printable PDF) -
-
- Emerson Electric Co.
- General Electric Company
- Honeywell International Inc.
- SKF Group
- National Instruments Corporation
- Parker Hannifin Corporation
- Rockwell Automation, Inc.
- Siemens AG
- ABB Ltd.
- Brüel & Kjær Vibro GmbH
- Meggitt PLC
- ALS Limited
- Analog Devices, Inc.
- Fluke Corporation
- Azima DLI Corporation