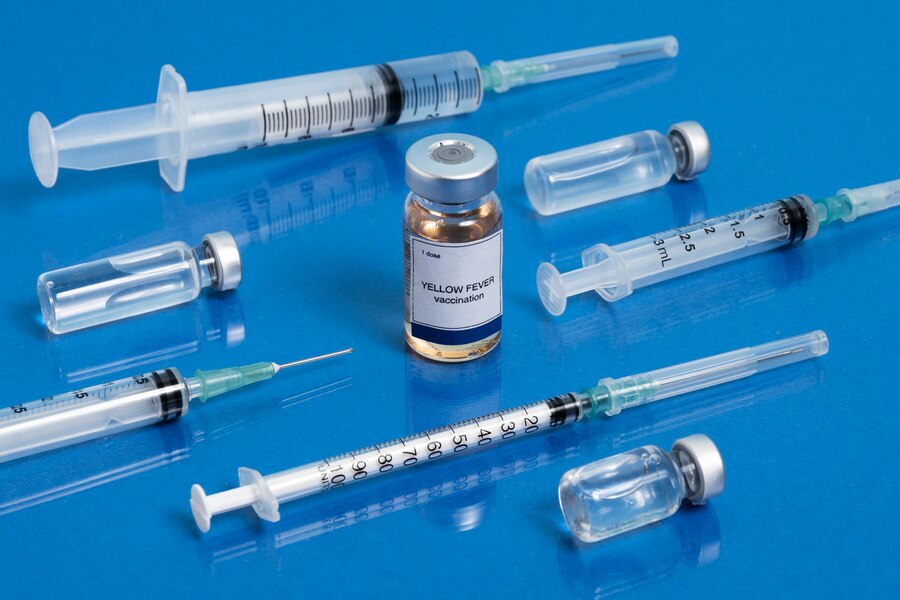
Plastic Injection Molding for Medical Device Market By Product (Polypropylene (PP), Acrylonitrile Butadiene Styrene (ABS), Polyethylene (PE), Polystyrene (PS), Polycarbonate (PC), Other Products), By Application (Medical Components, Implants, Cleanroom Supplies, Mobility Aids, Other Applications), By Region And Companies - Industry Segment Outlook, Market Assessment, Competition Scenario, Trends, And Forecast 2024-2033
-
18043
-
July 2024
-
300
-
-
This report was compiled by Trishita Deb Trishita Deb is an experienced market research and consulting professional with over 7 years of expertise across healthcare, consumer goods, and materials, contributing to over 400 healthcare-related reports. Correspondence Team Lead- Healthcare Linkedin | Detailed Market research Methodology Our methodology involves a mix of primary research, including interviews with leading mental health experts, and secondary research from reputable medical journals and databases. View Detailed Methodology Page
-
Quick Navigation
Report Overview
The Plastic Injection Molding for Medical Device Market was valued at USD 24.9 billion in 2023. It is expected to reach USD 38.6 billion by 2033, with a CAGR of 4.6% during the forecast period from 2024 to 2033.
The Plastic Injection Molding for Medical Device Market refers to the industry segment specializing in producing medical components and devices through plastic injection molding techniques. This process involves injecting molten plastic into a mold to create intricate and precise parts used in various medical applications, including surgical instruments, diagnostic devices, and implantable components. The market's growth is driven by increasing demand for minimally invasive medical procedures, advancements in polymer technologies, and the need for cost-effective, high-volume production of medical devices.
The Plastic Injection Molding for Medical Device Market is poised for significant growth, driven by several key factors. The increasing prevalence of chronic diseases and an aging global population are primary catalysts, as these demographics necessitate a higher demand for medical devices. The plastic injection molding process is critical in the production of these devices due to its ability to produce complex shapes with high precision and repeatability. Continuous advancements in injection molding technologies, including micro-molding and multi-material molding, are also enhancing production efficiency and the quality of medical devices. These technological innovations not only streamline manufacturing processes but also contribute to the development of more sophisticated and reliable medical devices.
However, the market does face challenges, notably the high initial costs associated with setting up injection molding facilities and machinery. This barrier to entry can be significant for new players attempting to penetrate the market. Despite this, ongoing research and development efforts are expected to mitigate these challenges by introducing advanced materials and innovative manufacturing processes. These developments are likely to further enhance the capabilities of plastic injection molding for medical devices, potentially reducing costs and improving the performance of the final products. As the market continues to evolve, stakeholders can expect a dynamic landscape where technological advancements and demographic trends drive demand, while ongoing innovations reduce barriers and improve production capabilities.
Key Takeaways
- Market Growth: The Plastic Injection Molding for Medical Device Market was valued at USD 24.9 billion in 2023. It is expected to reach USD 38.0 billion by 2033, with a CAGR of 4.6% during the forecast period from 2024 to 2033.
- By Product: Polypropylene (PP) dominated medical plastic injection molding market.
- By Application: Medical Components dominated the plastic injection molding market.
- Regional Dominance: North America dominates the Plastic Injection Molding for Medical Device Market with a 35% largest share.
- Growth Opportunity: The global plastic injection molding for medical devices market will grow in 2024 due to chronic diseases and biocompatible plastics advancements.
Driving factors
Increasing Demand for Medical Devices
The rising demand for medical devices significantly drives the growth of the plastic injection molding market for medical devices. This surge can be attributed to an aging population, increased prevalence of chronic diseases, and technological advancements in the healthcare sector. As the global population ages, the need for various medical devices such as syringes, diagnostic equipment, and surgical instruments grows. For instance, the report estimates that by 2030, one in six people in the world will be aged 60 years or over, leading to higher demand for healthcare services and, consequently, medical devices. This demand fuels the plastic injection molding market, as it is a preferred method for manufacturing precise and high-volume medical components.
Advancements in Material Science
Advancements in material science play a crucial role in the expansion of the plastic injection molding market for medical devices. The development of new biocompatible and medical-grade plastics has enhanced the performance and safety of medical devices. Innovations in polymers such as Polyether Ether Ketone (PEEK), thermoplastic elastomers, and biodegradable plastics have expanded the applications of plastic injection molding in the medical field. These materials offer superior mechanical properties, chemical resistance, and stabilizability, making them ideal for manufacturing complex and reliable medical components. According to a report, the global medical plastics market is expected to grow from USD 25.1 billion in 2020 to USD 31.8 billion by 2025, indicating the growing importance of material advancements in driving market growth.
Demand for Minimally Invasive Surgical Procedures
The increasing preference for minimally invasive surgical procedures is another critical factor propelling the growth of the plastic injection molding market for medical devices. Minimally invasive surgeries (MIS) are associated with reduced patient trauma, shorter recovery times, and lower healthcare costs. This trend has led to the development and adoption of specialized medical devices such as catheters, endoscopic instruments, and laparoscopic tools, many of which are produced using plastic injection molding. The rise in MIS is driven by technological advancements and the increasing awareness among patients and healthcare providers about the benefits of these procedures. A study highlights that the minimally invasive surgery market is expected to reach USD 44.6 billion by 2025, reflecting a compound annual growth rate (CAGR) of 6.7%. This growing market creates substantial opportunities for plastic injection molding manufacturers to supply high-precision, cost-effective medical devices.
Restraining Factors
Material Selection: Balancing Performance and Compliance in Medical Devices
Material selection plays a crucial role in the growth of plastic injection molding for the medical device market. The choice of materials affects not only the performance and durability of medical devices but also their compliance with stringent regulatory standards. Medical-grade plastics, such as polycarbonate, polyethylene, and polypropylene, are commonly used due to their biocompatibility, stabilizability, and mechanical properties.
The ability to select appropriate materials directly impacts the functionality and safety of medical devices. High-performance materials ensure that devices can withstand the sterilization process, maintain structural integrity, and exhibit the necessary chemical resistance. This is particularly important for devices used in invasive procedures where failure can have severe consequences.
Mold Steel Quality: Ensuring Precision and Longevity in Medical Device Production
The quality of mold steel is another critical factor influencing the growth of plastic injection molding for the medical device market. High-quality mold steel ensures the precision and longevity of molds, which are essential for producing complex and high-precision medical devices. The use of premium-grade steel, such as stainless steel or hardened tool steel, can significantly reduce maintenance costs and downtime, enhancing production efficiency.
The precision of molds directly affects the quality of the final medical device. Inaccurate molds can lead to defects, impacting the device's performance and safety. This is particularly crucial for medical devices that require high precision, such as surgical instruments, diagnostic devices, and implantable devices. The use of high-quality mold steel can ensure that the dimensions and tolerances of the molded parts meet the stringent requirements of the medical industry.
Furthermore, the durability of the mold steel impacts the production lifecycle. High-quality steel can withstand the wear and tear of high-volume production, reducing the need for frequent mold replacements. This not only lowers the operational costs but also ensures consistent product quality over time.
By Product Analysis
In 2023, Polypropylene (PP) dominated medical plastic injection molding.
In 2023, Polypropylene (PP) held a dominant market position in the by-product segment of the Plastic Injection Molding for Medical Device Market. Known for its excellent chemical resistance and high flexibility, PP accounted for a significant market share due to its widespread use in syringes, medical pouches, and diagnostic devices. Acrylonitrile Butadiene Styrene (ABS) followed closely, benefiting from its robust mechanical properties and superior impact resistance, making it ideal for housing and enclosures of electronic medical devices. Polyethylene (PE) also held a substantial share, particularly in the production of tubing and disposable medical products, thanks to its ease of processing and chemical inertness.
Polystyrene (PS) continued to be a preferred choice for single-use labware, such as Petri dishes and test tubes, due to its clarity and rigidity. Meanwhile, Polycarbonate (PC) carved out its niche in applications requiring high strength and transparency, like blood oxygenators and IV connectors. The Other Products category, encompassing materials such as Polyether Ether Ketone (PEEK) and thermoplastic elastomers (TPE), captured the remaining market share, driven by their specialized applications in surgical instruments and orthopedic devices. The diverse material properties within this segment underline the importance of tailored solutions to meet the stringent demands of the medical device industry.
By Application Analysis
In 2023, Medical Components dominated the plastic injection molding market.
In 2023, Medical Components held a dominant market position in the plastic injection molding for medical device market, accounting for the largest share in the by-application segment. This dominance can be attributed to the increasing demand for precision-engineered medical components used in a variety of devices such as syringes, catheters, and diagnostic equipment. The rise in chronic diseases and the aging population have fueled the need for reliable and high-quality medical components, thereby driving market growth.
Implants also represented a significant segment, driven by advancements in biocompatible materials and the growing acceptance of minimally invasive surgical procedures. The demand for custom and complex implant designs has further propelled the use of plastic injection molding in this sector.
Cleanroom supplies, essential for maintaining contamination-free environments in medical facilities, have seen a surge in demand. The precision and hygiene standards required in the production of these supplies have made plastic injection molding a preferred manufacturing method.
Mobility aids, including wheelchairs and prosthetics, have benefited from the customization and lightweight properties offered by plastic injection molding. This segment's growth is supported by the increasing prevalence of mobility impairments and technological advancements in assistive devices.
Other applications, such as packaging and disposable medical products, have also contributed to the market's expansion, driven by the need for cost-effective and scalable production solutions in the medical field.
Key Market Segments
By Product
- Polypropylene (PP)
- Acrylonitrile Butadiene Styrene (ABS)
- Polyethylene (PE)
- Polystyrene (PS)
- Polycarbonate (PC)
- Other Products
By Application
- Medical Components
- Implants
- Cleanroom Supplies
- Mobility Aids
- Other Applications
Growth Opportunity
Rise in Chronic Diseases and Aging Population
The global plastic injection molding for medical device market is poised for significant growth driven primarily by the increasing prevalence of chronic diseases and the aging population. As the world grapples with a rising incidence of conditions such as diabetes, cardiovascular diseases, and respiratory disorders, there is an escalating demand for medical devices that facilitate effective management and treatment. This surge in demand necessitates the production of high-quality, durable, and cost-effective medical devices, a need efficiently met by plastic injection molding. The technique's ability to produce complex shapes with high precision and consistency makes it ideal for manufacturing a wide range of medical components, from diagnostic devices to surgical instruments.
Advancements in Biocompatible Plastics
Another critical factor contributing to the market's growth is the advancement in biocompatible plastics. Innovations in this area have led to the development of materials that not only meet stringent medical standards but also offer enhanced performance characteristics such as improved durability, flexibility, and resistance to chemicals. These advancements are crucial for ensuring the safety and efficacy of medical devices, thereby boosting their adoption across healthcare settings. Biocompatible plastics are particularly important in applications requiring direct contact with human tissues and fluids, such as catheters, implants, and prosthetics. The enhanced properties of these materials, coupled with their compatibility with plastic injection molding processes, present significant opportunities for market expansion.
Latest Trends
Automation and Smart Manufacturing
The plastic injection molding for medical devices market is expected to experience significant advancements due to the adoption of automation and smart manufacturing technologies. Automation is streamlining production processes, reducing labor costs, and enhancing precision in medical device manufacturing. Smart manufacturing, integrated with Industry 4.0 principles, employs IoT, AI, and machine learning to enable real-time monitoring, predictive maintenance, and efficient quality control. This transformation is not only boosting production efficiency but also minimizing errors and ensuring higher consistency and reliability of medical devices. As a result, companies leveraging these technologies are likely to gain a competitive edge, driving overall market growth.
Sustainability and Eco-Friendly Practices
The emphasis on sustainability and eco-friendly practices within the plastic injection molding market for medical devices is anticipated to intensify. Growing environmental concerns and stringent regulatory frameworks are compelling manufacturers to adopt greener production methods. This includes using biodegradable and recyclable materials, reducing waste, and improving energy efficiency throughout the manufacturing process. Sustainable practices are not only aligning with global environmental goals but also appealing to environmentally conscious consumers and healthcare providers. Companies that prioritize sustainability are expected to enhance their brand reputation and meet the increasing demand for eco-friendly medical devices, fostering market expansion.
Regional Analysis
North America dominates the Plastic Injection Molding for Medical Device Market with a 35% largest share.
The Plastic Injection Molding for Medical Device Market demonstrates significant regional variability in demand and production capabilities. North America leads the market, commanding approximately 35% of the global share. This dominance is attributed to the advanced healthcare infrastructure, high investment in medical technology, and the presence of key industry players such as Medtronic and Johnson & Johnson. Europe follows closely, holding about 30% of the market share, driven by stringent regulatory standards and a robust medical device manufacturing sector, particularly in countries like Germany and France.
In the Asia Pacific region, the market is experiencing rapid growth, accounting for around 25% of the global share. This growth is fueled by increasing healthcare expenditures, a burgeoning middle-class population, and a shift of manufacturing bases to countries like China and India due to cost advantages. The Middle East & Africa and Latin America regions, while smaller in market share, collectively represent approximately 10% of the market. These regions are gradually expanding due to improving healthcare infrastructures and increasing foreign investments. The Middle East, in particular, is witnessing growth due to rising demand for advanced medical devices in countries like the UAE and Saudi Arabia. Overall, North America remains the dominant region, driven by technological advancements and substantial investments in the healthcare sector.
Key Regions and Countries
North America
- The US
- Canada
- Rest of North America
Europe
- Germany
- France
- The UK
- Spain
- Netherlands
- Russia
- Italy
- Rest of Europe
Asia-Pacific
- China
- Japan
- Singapore
- Thailand
- South Korea
- Vietnam
- India
- New Zealand
- Rest of Asia Pacific
Latin America
- Mexico
- Brazil
- Rest of Latin America
Middle East & Africa
- Saudi Arabia
- South Africa
- UAE
- Rest of the Middle East & Africa
Key Players Analysis
The global Plastic Injection Molding for Medical Device Market is projected to experience substantial growth in 2024, driven by advancements in medical technology and increasing demand for precise and high-quality medical devices. Leading the market are prominent companies such as Dow, Inc., SABIC, and Eastman Chemical Company, which are known for their innovative materials and extensive expertise in the field.
Dow, Inc. is expected to maintain its strong market position through continuous innovation in polymer technology and strategic collaborations with medical device manufacturers. SABIC, leveraging its robust research and development capabilities, is anticipated to enhance its product offerings, focusing on biocompatibility and sustainability, which are critical in medical applications.
Eastman Chemical Company is likely to gain a competitive edge by expanding its portfolio of specialty polymers designed for medical applications, ensuring high performance and regulatory compliance. Covestro AG's focus on developing high-quality polycarbonate materials that meet stringent medical standards is projected to strengthen its market share.
Smaller players like Rutland Plastic and Evonik Industries AG are also expected to contribute significantly by offering niche solutions and customized products, catering to specific medical device needs. Sumitomo Chemical Co., Ltd., and Arkema are poised to leverage their global presence and technical expertise to capture new market opportunities, while INEOS Group is likely to focus on expanding its manufacturing capabilities to meet growing demand.
Overall, the market is expected to be characterized by innovation, strategic partnerships, and a focus on meeting regulatory requirements, with key players driving growth through their advanced material solutions and commitment to quality and sustainability.
Market Key Players
- Dow, Inc.
- SABIC
- Eastman Chemical Company
- Covestro AG
- Rutland Plastic
- Evonik Industries AG
- Sumitomo Chemical Co., Ltd.
- Arkema
- INEOS Group
- Other Key Players
Recent Development
- In March 2024, Micro Systems significantly expanded its capabilities in medical plastic injection molding, focusing on ultra-precision injection molds for the medical, pharmaceutical, diagnostics, and ophthalmic markets. This expansion aims to enhance production efficiency and product quality, particularly in the manufacturing of micro and nano-feature medical components.
- In January 2024, GW Plastics announced a strategic collaboration with a leading medical device company to develop advanced injection molding technologies. This partnership focuses on integrating 3D printing with traditional injection molding processes to produce complex medical devices with higher precision and reduced manufacturing time.
- In February 2024, Protolabs introduced new innovations in medical device components using plastic injection molding. These innovations include the development of biocompatible and bioresorbable polymers aimed at improving patient safety and device performance. The company is also focusing on creating smaller, more intricate components suitable for the latest medical technologies.
Report Scope
Report Features Description Market Value (2023) USD 24.9 Billion Forecast Revenue (2033) USD 38.6 Billion CAGR (2024-2032) 4.6% Base Year for Estimation 2023 Historic Period 2016-2023 Forecast Period 2024-2033 Report Coverage Revenue Forecast, Market Dynamics, COVID-19 Impact, Competitive Landscape, Recent Developments Segments Covered By Product (Polypropylene (PP), Acrylonitrile Butadiene Styrene (ABS), Polyethylene (PE), Polystyrene (PS), Polycarbonate (PC), Other Products), By Application (Medical Components, Implants, Cleanroom Supplies, Mobility Aids, Other Applications) Regional Analysis North America - The US, Canada, Rest of North America, Europe - Germany, France, The UK, Spain, Italy, Russia, Netherlands, Rest of Europe, Asia-Pacific - China, Japan, South Korea, India, New Zealand, Singapore, Thailand, Vietnam, Rest of Asia Pacific, Latin America - Brazil, Mexico, Rest of Latin America, Middle East & Africa - South Africa, Saudi Arabia, UAE, Rest of Middle East & Africa Competitive Landscape Dow, Inc., SABIC, Eastman Chemical Company, Covestro AG, Rutland Plastic, Evonik Industries AG, Sumitomo Chemical Co., Ltd., Arkema, INEOS Group, Other Key Players Customization Scope Customization for segments, region/country-level will be provided. Moreover, additional customization can be done based on the requirements. Purchase Options We have three licenses to opt for Single User License, Multi-User License (Up to 5 Users), Corporate Use License (Unlimited User and Printable PDF) -
-
- Dow, Inc.
- SABIC
- Eastman Chemical Company
- Covestro AG
- Rutland Plastic
- Evonik Industries AG
- Sumitomo Chemical Co., Ltd.
- Arkema
- INEOS Group
- Other Key Players